برای اولین بار در کشور به بهره برداری رسید؛
بومی سازی و جایگزینی ۱۶ پایۀ هیدروژنی و اتوماسیون صنعتی در فولاد مبارکه
دکترسبحانی مدیرعامل شرکت فولاد مبارکه با ابراز خرسندی از اجرای موفقیت آمیز این پروژه گفت: بهره برداری از این طرح که سالانه بیش از ۷۰ هزار تن افزایش ظرفیت تولید محصولات ویژه در نورد سرد فولاد مبارکه را در پی دارد، مصداق بارز به بار نشستن راهبردهای اقتصاد مقاومتی، قطع وابستگی و گام برداشتن صحیح در مسیر تولید و اشتغال است.
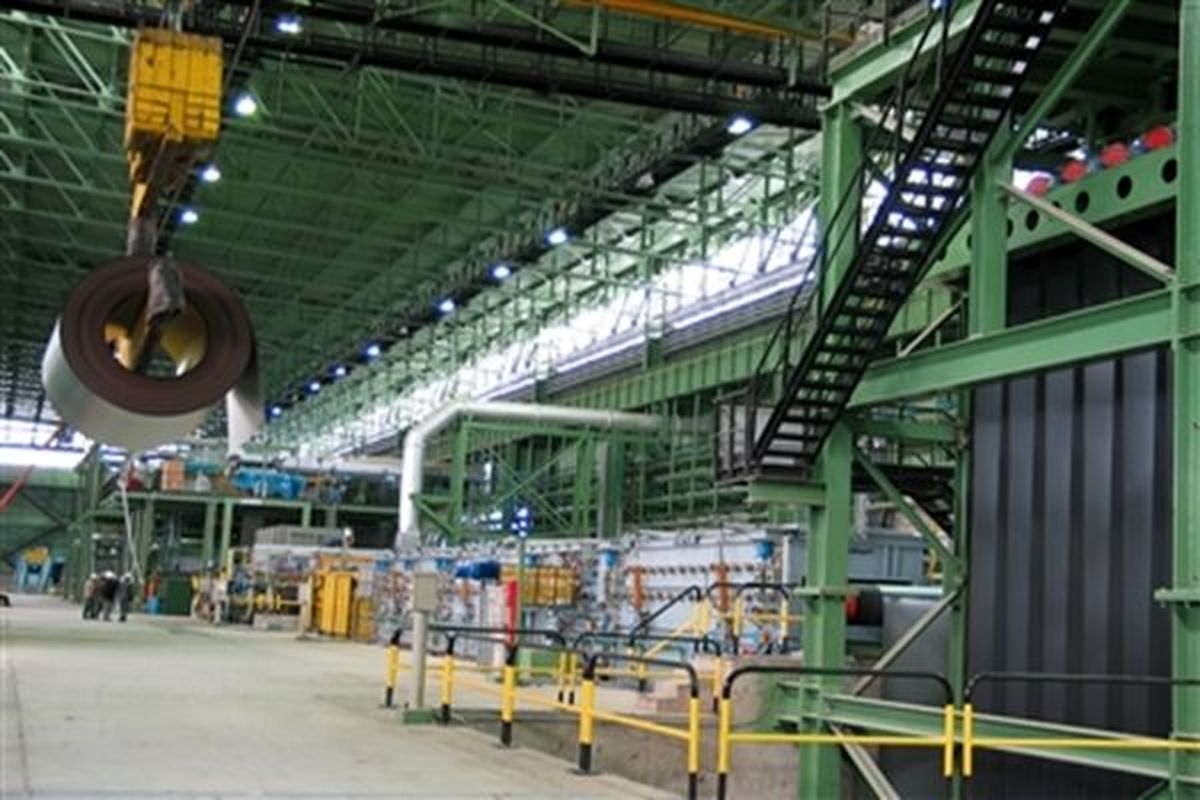
به گزارش خبرگزاری موج، پروژۀ بومی سازی و جایگزینی ۱۶ عدد پایۀ هیدروژنی به جای پایه های HNX و اتوماسیون صنعتی در واحد باکس آنیلینگ نورد سرد شرکت فولاد مبارکه به دست توانمند کارکنان فولاد مبارکه و با مشارکت شرکتهای داخلی با موفقیت پایان یافت و با حضور دکتر سبحانی مدیرعامل، معاونان، جمعی از مدیران فولاد مبارکه و مدیـــــران عامل شـــــرکتهای پیمانکاری حاضر در این پروژه به بهره برداری رسید.
اجرای این پروژه نماد عینی هماهنگی، خودباوری و ترجمۀ «ما میتوانیم» است
در این مـــراسم دکترسبحانی مدیرعامل شرکت فولاد مبارکه با ابراز خرسندی از اجرای موفقیت آمیز این پروژه گفت: بهره برداری از این طرح که سالانه بیش از ۷۰ هزار تن افزایش ظرفیت تولید محصولات ویژه در نورد سرد فولاد مبارکه را در پی دارد، مصداق بارز به بار نشستن راهبردهای اقتصاد مقاومتی، قطع وابستگی و گام برداشتن صحیح در مسیر تولید و اشتغال است.
وی با تأکید بر اینکه انجام این پروژۀ بزرگ که برای اولین بار در کشور انجام شد ریسک بالایی را نیز به همراه داشت، افزود: خوشبختانه مدیریت و کارشناسان فولاد مبارکه با اتکا به دانش فنی و خلاقیت خود و با همکاری بسیار خوب پیمانکاران و شرکتهای سازنده داخلی توانستند شجاعانه و با جسارت هرچه تمام تر این مهم را انجام دهند.
مدیرعامل فولاد مبارکه با اشاره به این مطلب که بهره برداری از این پروژه علاوه بر اینکه ارتقای سطح کمی و کیفی محصولات این ناحیه را در برداشته و کشور ایران را نیز در دستیابی به یکی دیگر از تکنولوژیهای عرصۀ صنعت فولاد رهنمون ساخته است، افزود: در هنگام تصمیم گیری برای آغاز این طرح بزرگ عوامل بازدارنده ای پیش رو بود و مجموعه را از انجام آن بر حذر میداشت، اما راهبردهای کلان کشور و تجارب مشابه فولاد مبارکه ما را دلگرم ساخت. نتیجۀ این حمایت ها و همدلی ها این شد که بار دیگر دانش فنی کشور و همچنین توان تولید کمی و کیفی نورد سرد فولاد مبارکه افزایش یافته است.
وی ضمن قدردانی از وفاق و همدلی حاکم بر شرکت و شرکای تجاری کسب و کار فولاد مبارکه، اظهار کرد: بومی سازی و جایگزینی ۱۶ عدد پایۀ هیدروژنی،۱۲ کوره و اتوماسیون صنعتی و بهره برداری از آنها علاوه بر ارتقای دانش فنی، حدود ۳۰۰ تا ۳۵۰ هزار یورو به ازای هر مجموعه پایه و کوره و... برای شرکت صرفه جویی به همراه داشته است. ضمن اینکه انجام این کار در داخل کشور علاوه بر اشتغالزایی و کاهش مصرف انرژی، استفاده از مواد مصرفی و کالای ایرانی را نیز به همراه داشته که از دیگر مزایای مهم اجرای این پروژه است.
ایشان در پایان با تأکید بر اینکه اجرای این پروژه نماد عینی هماهنگی، خودباوری و ترجمۀ «ما میتوانیم» است، از تمامی تلاشگران حاضر در این پروژه قدردانی و خاطرنشان کرد: این اقدامات می تواند به عنوان یک الگو در کشور به کار گرفته شود.
جسارت و مسئولیت پذیری کارکنان و پیمانکاران دو شاخص مهم در اجرای این پروژه
در این باره مختار بخشیان، معاون بهره برداری فولاد مبارکه نیز با اشاره به عوامل مؤثر در کسب این موفقیت گفت: جسارت و مسئولیت پذیری کارکنان و پیمانکاران مجری این طرح باعث شد علیرغم همۀ موانع و ریسکهای احتمالی، امروز شاهد به بار نشستن تمامی زحمات و بهره برداری از این پروژه باشیم.
وی از دستیابی به دانش فنی بومی سازی و جایگزینی ۱۶ عدد پایه هیدروژنی و اتوماسیون صنعتی در این پروژه به عنوان مهمترین دستاورد این طرح یاد کرد و از همه دستاندرکاران و مجریان آن قدردانی کرد.
تجهیزات بومیسازی شده با کاهش مصرف انرژی و بدون هیچ مشکلی در حال تولید هستند
این گزارش حاکی اســت، نادر حسین زاده، مدیر ناحیۀ نورد سرد نیز گفت: امروز در ناحیۀ نورد سرد شرکت فولاد مبارکه شاهد بهره برداری از پروژه ای هستیم که حاصل دو سال تلاش شبانه روزی مدیریت و کارکنان فولاد مبارکه و شرکای تجاری کسب وکار این شرکت است. این در حالی است که تمام فعالیتهای انجام شده در این راستا از ابتدا تا انتها به دست توانای کارکنان داخلی بومی سازی شده و به بهره برداری رسیده است.
وی در تشریح ضرورت و اهمیت اجرای این پروژه، تصریح کرد: با توجه به افزایش تقاضای بازار برای ورق های ویژه و طولانی بودن سیکل آنیل این گریدها و نبود ظرفیت کافی در این بخش، این واحد به گلوگاهی در تولید محصولات سرد مبدل شده است؛ بنابراین توسعۀ واحد بازپخت هیدروژنی در ناحیۀ نورد سرد اجتناب ناپذیر بود؛ ازاین رو در شرایط تحریم و قطع همکاری شرکتهای خارجی، مدیریت فولاد مبارکه بر آن شد تا نسبت به انجام پروژۀ جایگزینی ۱۶ عدد پایه هیدروژنی به جای پایه های HNX اقدام کند.
وی افزود: عملیات اجرایی این پروژه از مهرماه سال ۹۴ آغاز و پیش بینی شد در یک بازۀ زمانی دوساله به اتمام برسد. خوشبختانه این امر محقق شد و هم اکنون پایه ها بدون هیچ مشکلی و با کاهش مصرف انرژی در حال تولید هستند.
مدیر ناحیه نورد سرد هزینۀ اجرای این پروژه را حدود ۲۹ میلیارد تومان اعلام کرد و یادآور شد: اجرای این پروژه با بهره گیری از توان داخل کشور، بیش از ۱۷ میلیارد تومان برای فولاد مبارکه صرفه جویی به همراه داشته است.
حسین زاده اهم فعالیتهای انجام شده در این پروژه را تهیۀ مدارک و مستندات ساخت تجهیزات موردنیاز در پروژه شامل پایه، کوره، کلاهک خنک کننده و برخی از قطعات یدکی، بررسی امکانات فولاد مبارکه جهت ساخت برخی از تجهیزات در داخل شرکت، بررسی امکانات شرکتهای داخلی جهت ساخت تجهیزات موردنیاز و همچنین بومی سازی و جایگزینی سیستم خودکارسازی صنعتی دانست و گفت: در بازۀ زمانی اجرای این پروژه با چالشهای جدی مواجه شدیم که هر بار با حمایت مدیریت عالی شرکت و با اتکا به دانش فنی داخلی فولاد مبارکه و پیمانکاران طرح، ازجمله شرکت های طراحان و مجریان فرایند بخار، ایریسا، تقطیران، صنایع برز قزوین، تامکار، دابو صنعت، سداد صنعت برطرف شد.
وی با تأکید بر اینکه تمامی این فعالیتها بدون هیچ توقفی در خطوط تولید انجام شد، گفت: میتوان از دمونتاژ تجهیزات قدیمی (پایه هایHNX) در هر دو واحد آنیلینگ ۱ و ۲، دمونتاژ تجهیزات ۱۶ عدد پایه به میزان ۱۵۰تن و ارسال به انبار ضایعات، دمونتاژ لوله های سیالات به میزان ۶۵۰ متر و وزن ۵۰ تن و ارسال به انبار ضایعات، پسکشی ۴۵۰۰ متر کابل قدرت و فرمان و همچنین مونتاژ تجهیزات جدید به عنوان بخش دیگری از این اقدامات نام برد.
وی با اشاره به اینکه اجرای این طرح بزرگ در سلامت کامل کارکنان و با ایمنی بالا انجام شد، از برگزاری ۱۲۰ نفر ساعت جلسۀ هماهنگی ایمنی در مراحل مختلف کاری، انجام ۱۳۰ نفر ساعت تست گازسنجی توسط بازرسان مرکز ایمنی، اجرای ۱۴۰۰۰ اینچ عملیات پایپینگ، تست RT و PT به میزان ۱۵۰۰ اینچ، ساخت ۶۴ دستگاه تابلوی برق، اجرای ۲۱۰۰۰ متر کابلکشی، اجرای ۹۰۰۰ کانکشن برق و ابزار دقیق، اجرای ۱۴۰۰ متر کاندوئیت برق، اجرای عملیات سیم بندی برای ۲۲۴۰ عدد INPUT و OUTPUT و تهیۀ ۱۰۰۰ برگ مستندات جهت شناخت سیستم اتوماسیون موجود و جدید در این راستا خبر داد.
حسین زاده با بیان اینکه اجرای این طرح علاوهبر ارتقای دانش فنی شرکت، در هر ماه به میزان ۶ هزار تن به ظرفیت تولید محصولات ویژه واحد باکس آنیلینگ اضافه کرد، تصریح کرد: از مهمترین دستاوردهای این طرح جامع میتوان به کاهش مصارف انرژی و سیالات به دلیل افزایش سرعت تولید ناشی از استفاده صددرصد گاز هیدروژن اشاره کرد.
حسین زاده در پایان از همۀ دست اندرکاران اجرای این طرح غرورآفرین ازجمله واحدهای تعمیرگاه مرکزی، واحد بومیسازی و مهندسی معکوس، واحد نسوز، خرید قطعات یدکی و ماشین آلات، واحد کنترل کیفیت قطعات یدکی، مرکز ایمنی و آتش نشانی، امور قراردادهای خرید، مدیریت حراست، بازرسی فنی خوردگی و ابزار دقیق، مهندسی کارخانه، مرکز ایمنی و آتشنشانی، تعمیرات مرکزی، واحد آنیل و شست وشو، دفاتر فنی تولید و تعمیرات و تعمیرات تخصصی ناحیۀ نورد سرد،، روابط عمومی، سایر همکاران ناحیۀ نورد سرد و تمامی شرکتهای پیمانکار یادشده تشکر و قدردانی کرد.
این مطلب، یک خبر آگهی بوده و در محتوای آن هیچ نظری ندارد.
ارسال نظر